A chip off the old engine block
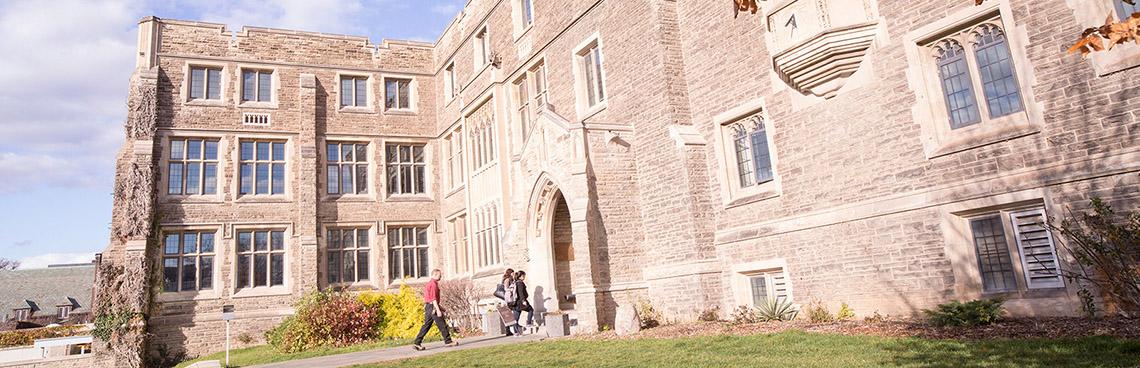
[img_inline align=”right” src=”http://padnws01.mcmaster.ca/images/Elbestawi2.jpg” caption=”Mo Elbestawi, dean of engineering at McMaster.”]The following is a partial transcript of an article that appeared in the November 2004 issue of AutoPlant Magazine
A research team led by engineers from McMaster University in Hamilton has developed a promising new automotive process to machine car engine blocks. The process is said to be faster, cheaper and better for the environment than existing methods.
The process relies on ultra-high speed machining and a high-pressure mixture of compressed air and synthetic oil. Researchers believe the McMaster engine block project will give the Canadian car industry a significant leg-up in global auto trade.
“It's important that (Canada) is always one step ahead in terms of technology,” states Mo Elbestawi, dean of engineering at McMaster.
Launched in 2001, the engine block project was conceived and co-ordinated by Elbestawi. While the project is not complete, he says the initial results have proven “better than expected.”
The engine block initiative was largely funded by AUTO21, a “Network of Centres of Excellence” based in Windsor, Ont. Networks of Excellence are partnerships between universities, industry, government and non-profit organizations. AUTO21 supports research on a wide variety of car-related subjects, from road rage and impaired driving to new manufacturing processes and materials.
“We want to fund world-class research to benefit the Canadian auto sector,” says Peter Frise, CEO and scientific director of AUTO21. “The fit (with Elbestawi) was obvious.”
In total, AUTO21 has provided roughly $1.4 million in funding for the McMaster engine block project. Additional support has come from various private corporations, such as General Motors and Ford Motors of Canada.
A total of roughly two dozen researchers from the University of Windsor, University of Waterloo, Ecole Polytechnique in Montreal and the University of New Brunswick have toiled on the engine block initiative, under the supervision of Elbestawi.
Much of the work was conducted at the McMaster Manufacturing Research Institute (MMRI), an advanced research laboratory. Created in 2000, the Institute specializes in research on metal cutting, polymer processing, robotics and machinery, among other subjects.
The McMaster team's research consisted of 20 per cent computer simulations and “80 per cent actual machining of engine blocks,” says Eu-Gene Ng, a research manager at the MMRI. “The computer simulation was employed to study the effects of machining parameters on burr formation and residual stress, and also to reduce the size of the test matrix.”
Many of the team's experiments centred on ultra-high speed machining techniques. “The technology of ultra-high speed machining has been around for some time, maybe half-a-dozen to 10 years,” states Elbestawi. “(However, we are) probably the only Canadian universityif not, then certainly one of two or threethat have the (right) equipment to actually work in this technology.”
According to Ng, the “majority of North American automotive industries employ cutting speeds of up to 2,000 metres per second.” And, through the use of ultra-high speed machining, the McMaster researchers were able to reach cutting speeds of 5,000 metres per second.
Cutting at such fast speeds has allowed the team to reduce the time required to cut an engine block by 150 per cent. It also resulted in high material removal rates, high productivity and helped generate good surface roughness.
Shorter cutting times will provide manufacturers with projected cost savings of more than 30 per cent.
The new process is also environmentally friendly. Traditional cutting methods gobble up large amounts of lubricant up to 60 litres per minute, explains Ng. The McMaster team, however, used a high-pressure mix of compressed air and synthetic oil for their tests. The new process used only five milliliters of oil per hour a 99 per cent decrease with ensuing benefits for the environment.
Disposing of traditional lubricant solutions is expensive and potentially dangerous to the environment. The small amount of oil used in the new process, however, is biodegradable. “There's no health hazard,” says Ng. “Workers are happy to work with it.”
The experiments also turned up some unexpected results. Elbestawi, for example, says he was pleasantly surprised at the “performance of some of the cutting tools,” which lasted much longer than expected.
The initial phase of the engine block project is expected to wrap up next spring. Meanwhile, a new phase of the project is currently under consideration.
(Source: AutoPlant Magazine)