posted on Nov. 21: Development of new materials for cars powers research in new centre
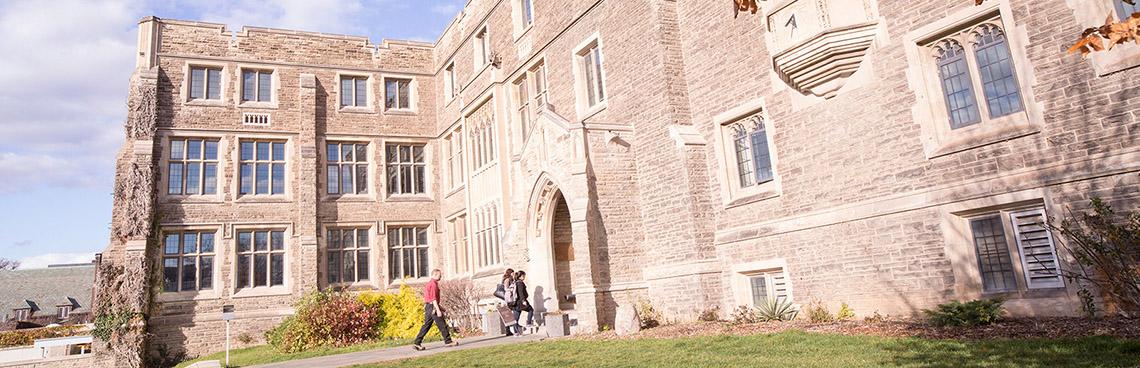
[img_inline align=”right” src=”http://padnws01.mcmaster.ca/images/Dr_Wilkinson_small.jpg” caption=”David Wilkinson”]The car in your future will be lighter and kinder to the environment.
Aluminum may make up the trunk, the side door panels or the lid of the car. Or your car may be a hybrid — powered by a gas engine and a rechargeable battery.
The key to ensuring these types of vehicles become commonplace is adapting the materials now used in cars to new uses or developing new materials with unique properties.
David Wilkinson, professor of materials science & engineering and acting department chair, believes the University's new leading-edge research centre for automotive materials will excel in both areas.
“There's been considerable interest in new materials for automotive applications for quite some time,” said Wilkinson, acting director of the newly established McMaster Centre for Automotive Materials (MCAM).
“The thrust is science-based manufacturing. The idea is to apply the scientific principles and quantitative understanding to materials and manufacturing processes. There will be a dramatic shift and a change in the level of activity in this area. It has increased our ability to work collaboratively with industry.”
$9-million centre
The $9-million research centre, which was established as part of a successful proposal to the Ontario Research and Development Challenge Fund, will also receive funding from Alcan, Inco, the Canada Foundation for Innovation, the Natural Sciences and Engineering Research Council and Materials and Manufacturing Ontario.
The centre's mandate is to conduct research on materials that are used in the automotive sector and involve the processing of materials, component fabrication and materials characterization and testing.
McMaster engineers and scientists were invited to work collaboratively with industrial partners and are affiliated with the Centre for Automotive Materials and Manufacturing (CAMM), also an ORDCF-funded centre, which is based at Queen's University's.
About 20 McMaster graduate students and full-time researchers will spend some of their time on campus and some in Kingston, conducting experiments at Alcan's Kingston Research and Development Centre.
The MCAM has already forged a strong link with the giant aluminum manufacturer.
Alcan gave the centre $2 million to boost research examining the use of aluminum sheeting in the manufacture of car body panels and the outer skin, such as doors, lids and trunks.
Drive for lighter vehicles
“The lighter those are, the easier they are to use,” said Wilkinson.
“If we can reduce the size, there is a further weight savings and cost savings. There is a real thrust driven by society to reduce the weight of vehicles and improve engine efficiency. We're back to making the vehicles lighter so you have less mass to move around.”
Right now, the main structural components of a car are made of steel. Wilkinson said the centre's researchers will be involved with the University's Steel Research Centre and Manufacturing Research Institute in studying how new grades of steel and higher-strength steel that requires less material can be optimized in the automotive sector.
The team is especially excited about exploring the benefits of aluminum. Aluminum is intrinsically lighter than steel, but it is harder to extract from the ore, so larger amounts of energy (primarily hydro-electric power) are required. On the other hand, Wilkinson said that secondary processing of aluminum is easier and less costly because it is done at a lower temperature.
Examining processes
“We'll be looking at processing techniques that can reduce the cost of aluminum and make it more competitive,” Wilkinson said.
One of the main areas of research will be examining the process of thin-strip casting, replacing the half-metre thick ingots produced by the conventional process with thin (10 mm) slabs. In either case, the material must be rolled down to a thickness of 1-2 mm.
“It's just like rolling dough, you make it thinner and thinner,” said Wilkinson. “The problem with metals is that the more you form the materials, the harder they become. It becomes impossible to do this at a lower temperature and has to be done hot. It costs close to $1 billion to build an integrated hot- and cold-rolling facility to process conventional ingots, so the capital equipment is very expensive.”
The new idea is to cast material directly from liquid into thin strips, 10 to 15 millimetres. “You would start off with a thin material and then reduce it by cold rolling,” he said. “This reduces the cost of the plant considerably to say, around $100 million. There's a tremendous cost savings affiliated with that.
“We're interested in having it as high strength as possible. The strength is achieved through mechanical and thermal processing. The challenge is can we produce materials of comparable quality using a cheaper process using thin strip casting?” he said.
Another research focus for the centre involves the materials found in rechargeable batteries, which are currently used mostly in laptop computers and power tools.
Light-weight rechargeable batteries
Researchers at the MCAM are working with nickel-producer Inco Ltd. to understand the processing of nickel powder used in rechargeable batteries that could be used in electric hybrid cars.
Wilkinson said there are some hybrid cars on the market already that have a small gas engine and a battery-driven electric drive. The gas engine is used to accelerate the vehicle and the electrically driven motor is used when coasting.
“You need a battery for this and these batteries have to be as light as possible and have high-energy density,” he said. “We're trying to develop these.”